How RMD:s unique platform works – a system of systems
Railway Metrics and Dynamics develops and sells a unique platform for real-time analysis and monitoring of both rolling stock and infrastructure. The solution enables proactive and predictive management of all types of assets. The unique software platform is the hub for data collection and analysis.
Railway Metrics and Dynamics develops and sells a system platform for analysing and monitoring transport and infrastructure in real time. The company has chosen to focus on the railway industry, such as locomotives, train cars, rails and other railway infrastructure, but the platform can also be used in other transport and infrastructure markets.
Railway Metrics and Dynamics AB (RMD) is a Swedish technology company based in Stockholm that develops and sells a cloud and real-time platform. The technology is patented and the solution is based on advanced algorithms and artificial intelligence.
The platform is currently used for asset management in the railway industry. Initially, RMD has chosen to focus on the railway industry, such as locomotives, wagons, rails and other railway infrastructure, but the platform can also be used for infrastructure such as bridges.
More efficient, safer and profitable railway operations
For those involved in the railway industry, RMD’s system enables transport to operate with greater efficiency, safety, punctuality and profitability.
Perhaps the most important thing about Railway Metrics and Dynamics is that it is not just about developing sensors and analysing huge amounts of data – it is also about having the expertise to truly understand the running dynamics and the interaction between railway wheels and rails.
RMD knows rail. They understand and explain the dynamics between wheels and rails and analyse the deviations to find the causes, and RMD’s platform is the only one on the market that covers the entire railway system – from fixed infrastructure to individual vehicles – with a single measurement device.
System of systems – a unique ecosystem
RMD’s platform is a unique ecosystem, best described as a system of systems. In simple terms, it is a collection of task-oriented and uniquely dedicated systems that together form a new, more complex system that offers even more functionality and performance than the sum of the individual systems.
At the heart of the RMD system platform is the PMU sensor. It identifies movement patterns in real time and measures acceleration in three dimensions. All these movements are verified using unique algorithms. The more data collected – and the more PMUs installed around the world – the better the analysis and the more efficient the system becomes.
The PMU sensor was patented in France, Germany, the UK, Sweden, Australia and the USA in 2016. Since then, it has been optimised for mass production and the first series has been delivered and installed at customers in Sweden and Switzerland.
Sensors communicate with the cloud
The Performance Monitoring Unit (PMU) is a real-time sensor that can be easily mounted, for example, on a railway bogie, i.e. the pairs of wheels that support the wagon. Each PMU sensor is equipped with a GPS and two accelerometers that measure movement in three dimensions.
The sensors communicate with the cloud via an internet connection. The sensor can be mounted in a variety of locations on wagons and locomotives without damaging the vehicles. It can be placed in various positions on a wagon or bogie frame, or mounted on a pantograph. Very strong magnets are used in all cases.
The PMU sensor has both a regular battery and a rechargeable battery connected to a solar cell. The life of the regular battery is approximately six years of continuous operation. The built-in solar cell and rechargeable battery allow data to be sent and received much more frequently.
Optimised power consumption
The key to the device’s long life is its ability to operate in sleep mode. If nothing unexpected happens, the sensor scans existing vibration data in the background until an anomaly is detected. The PMU sensor has built-in microcontrollers and a CPU with integrated RAM and program memory.
The PMU sensor is designed to optimise power consumption while being able to detect anything that could potentially be wrong. This means that it ‘wakes up’ to transmit unexpectedly collected data, or for scheduled communication and synchronisation with the cloud.
PMU sensors can also be used to monitor fixed infrastructure, such as railway bridges. By placing a sensor on a bridge, you know in real time when a train is approaching because that train also has a PMU. This makes it possible to capture the interaction between the bridge structure and the train.
Machine Learning Lab builds solutions for the future
Railway Metrics and Dynamics has its own Machine Learning Lab in Stockholm for continuous development of algorithms, AI models and software. It includes all the hardware needed to develop the platform in the best possible way, servers for data storage and computation, a complete workshop for creating and assembling tools and equipment for collecting data, and a creative office space for cultivating new ideas.
The algorithms require constant development, and intensive work is currently underway as part of an innovation tender for the Swedish Transport Administration, where they will be used to detect and predict faults in signals and overhead lines. A new patent for use on pantographs has also been granted to Sweden.
The Machine Learning Lab serves as a central point and base for all RMD’s initiatives. The main advantage of the lab is that RMD has a place where it can consolidate experience and expertise and build for the future. Stockholm also offers Sweden’s broadest expertise in the field.
But most importantly, we have the right mix: unique expertise from the railway industry combined with unique expertise in data analytics and machine learning. We are truly pioneers in the industry.
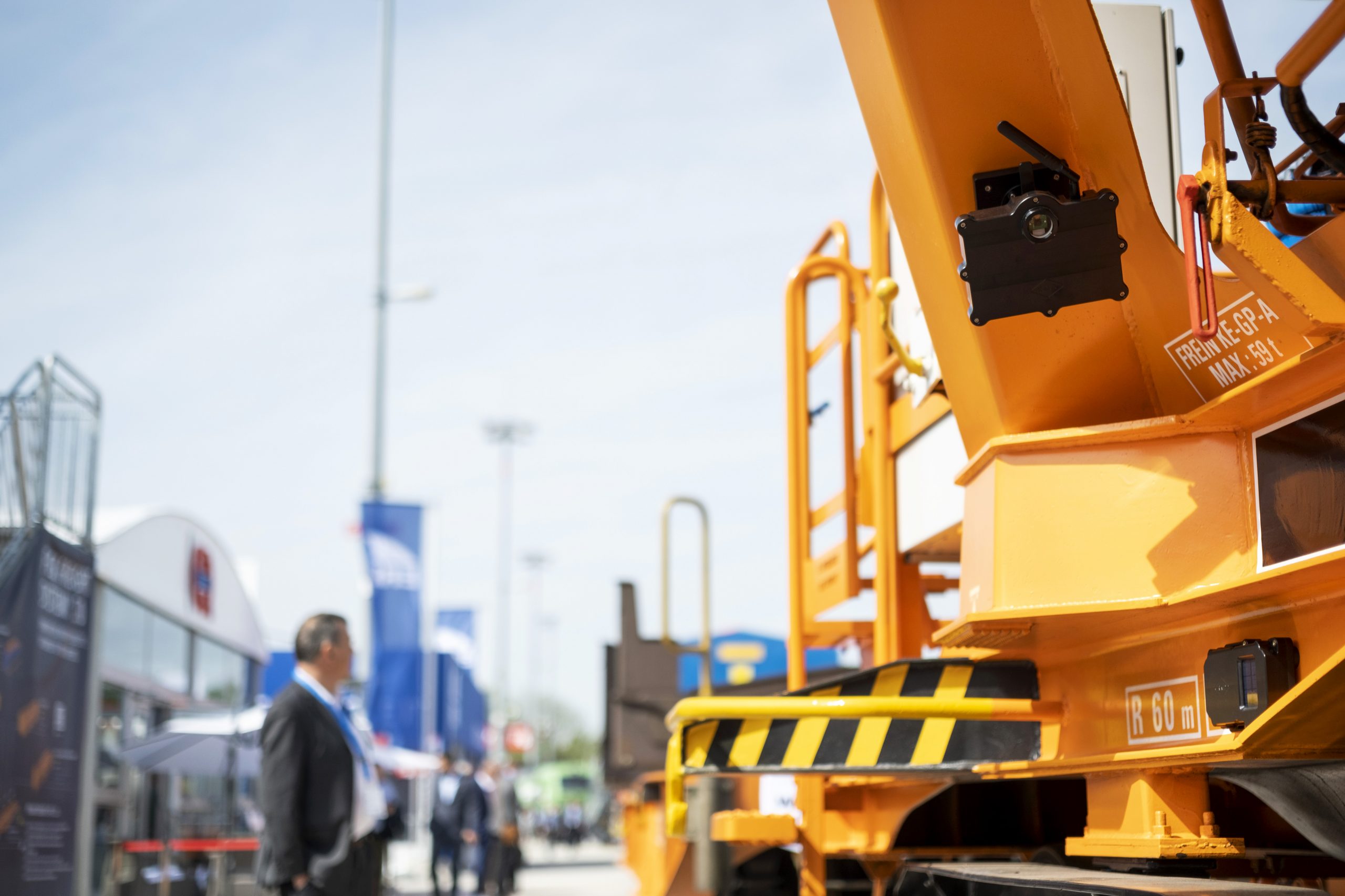
The Fanps 2.0 automated ballast wagon was on display at the Transport Logistics Fair in Munich on 9-12 May 2023. The picture also shows RMD’s rail camera and PMU sensor.
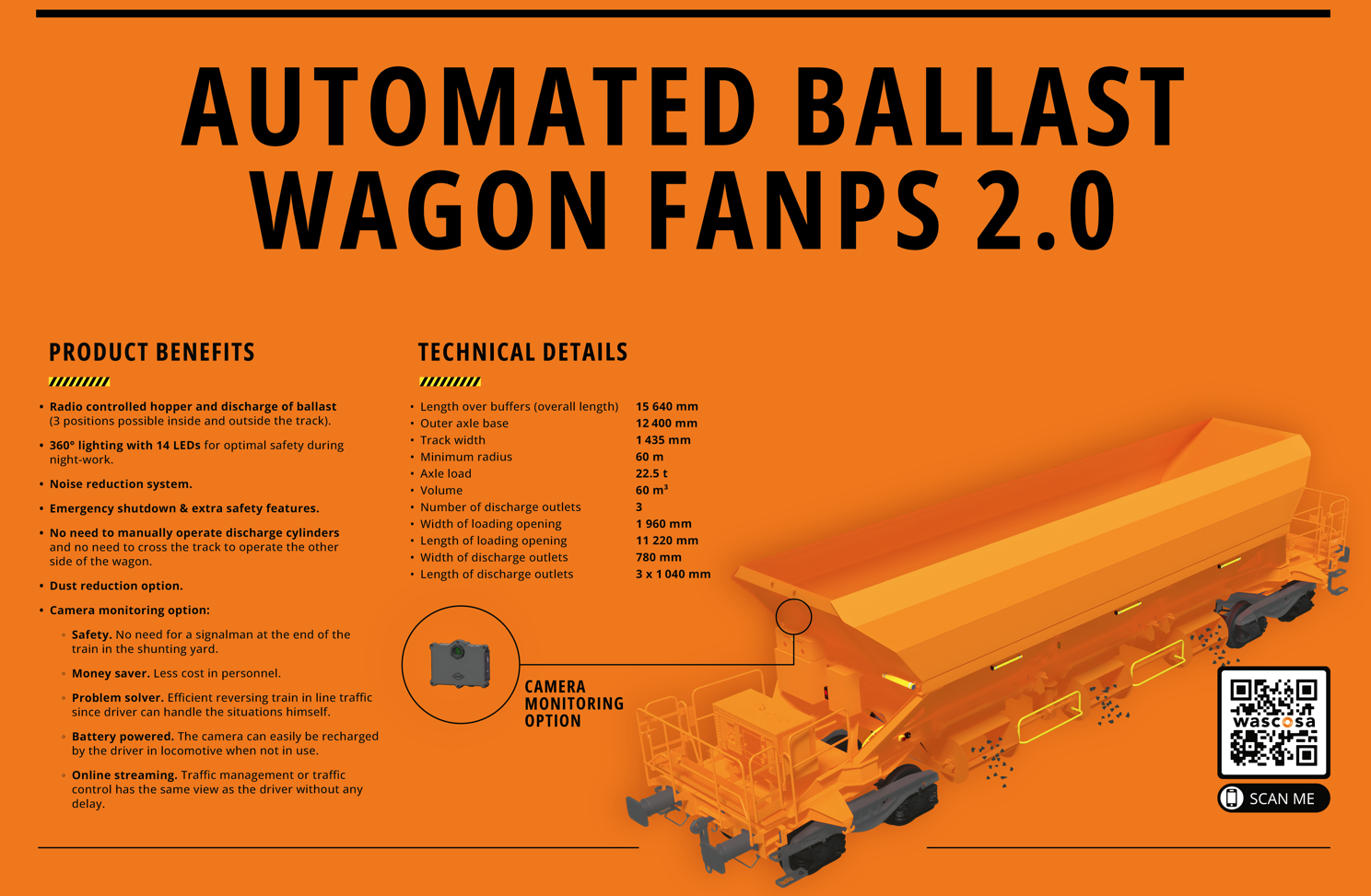
The railway camera was presented at the major infrastructure fair Transport Logistic in Munich as a selling innovation together with Wascosa and its new ballast wagon.
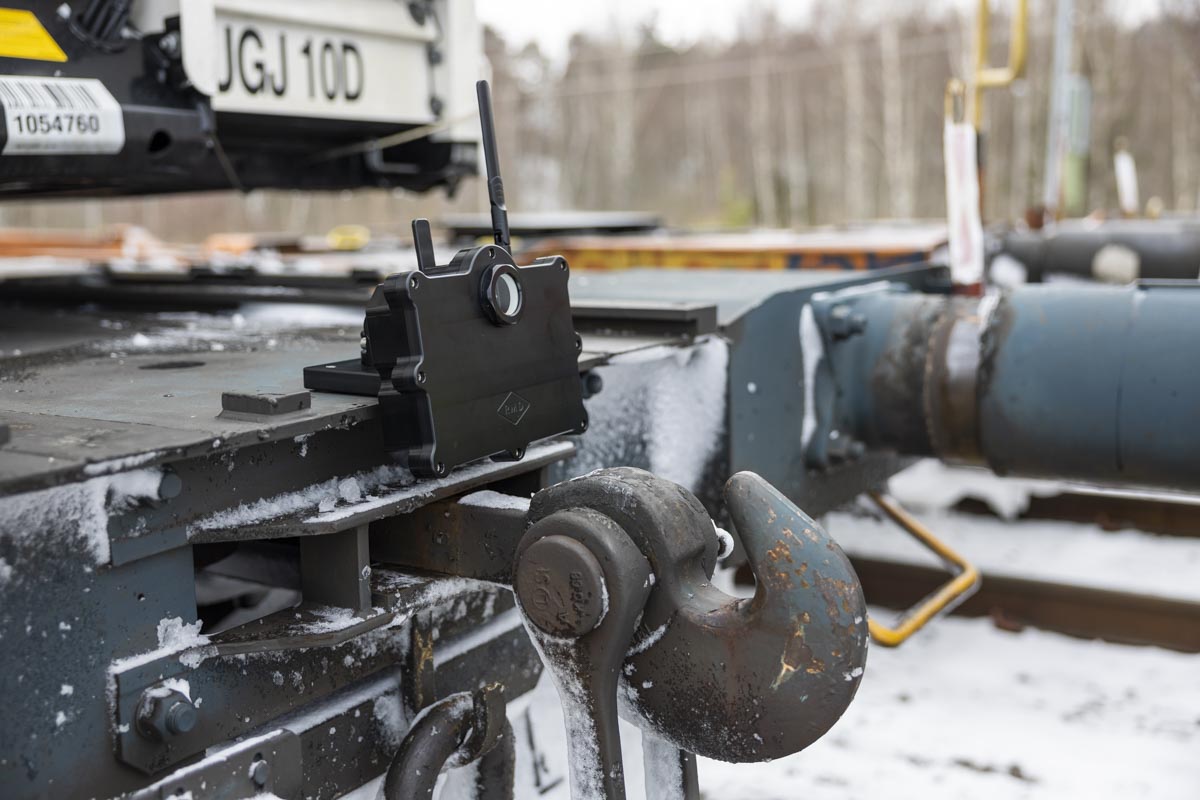
The railway camera mounted with a strong magnet at the back of a freight train.
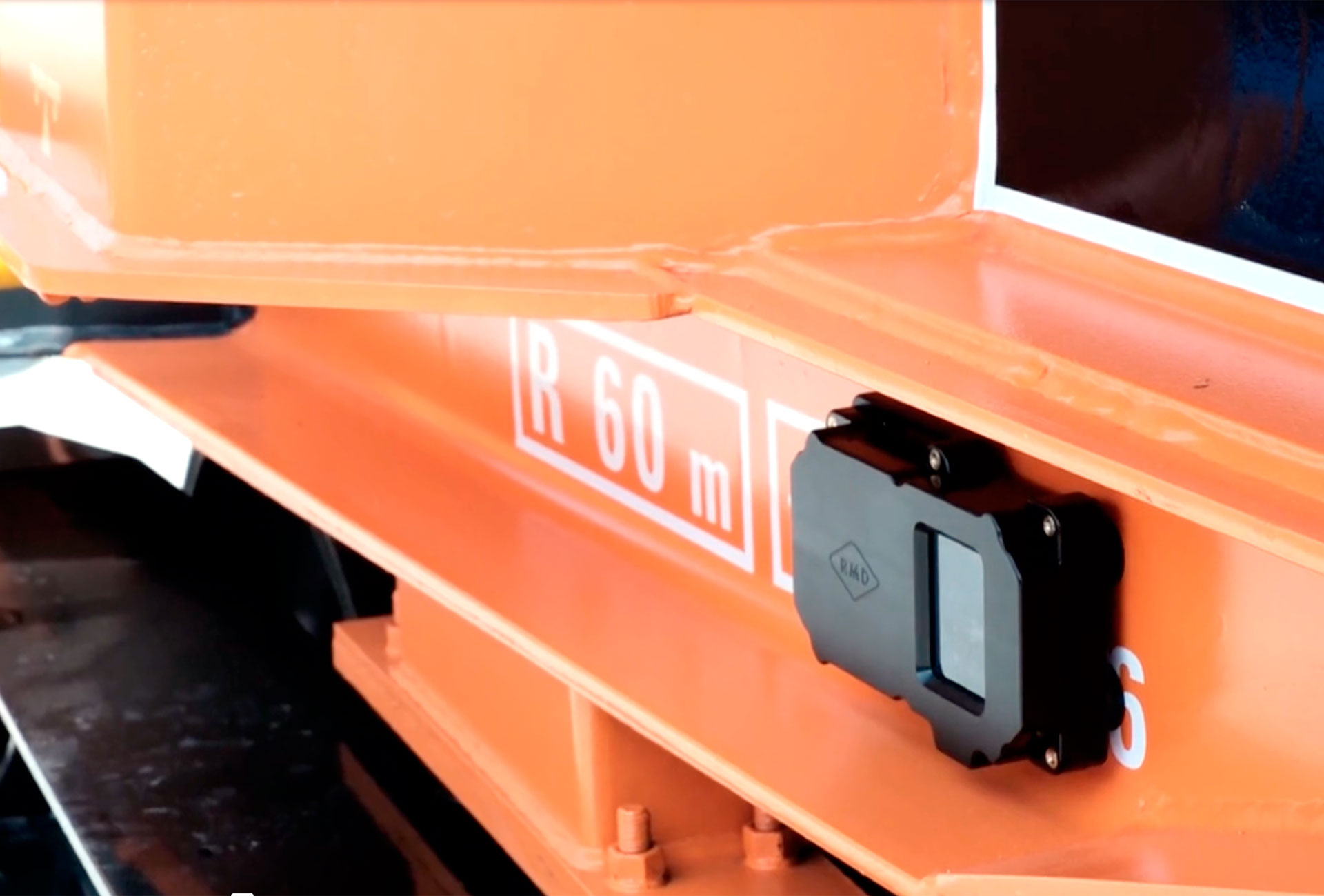
The latest version of the PMU sensor has been supplemented with a built-in solar cell and a rechargeable battery, allowing data to be sent and received much more frequently.
The railway camera as a key safety asset
The railway camera is unique in its kind and can be easily used by the driver, for example when the train needs to reverse. The potential for the reversing camera is huge. Most railway companies have a need for such a solution.
Thanks to real-time image transmission, the driver can also use the camera when reversing. The camera image appears on the RMD dashboard when mounted at the rear of the train, eliminating the need for an additional person/signaller standing unprotected at the rear of the train. This has significant safety benefits.
The railway camera uses WebRTC technology, which means it transmits video to the RMD Dashboard in real time, as long as there is an internet connection. This technology is supported by all major platforms and modern browsers. The railway camera is battery powered and can be recharged by the driver in the cab when not in use.
Another unique aspect is that traffic management or others who need to view the images can simultaneously access the video stream from anywhere using our dashboard.
All train movements are stored for as long as the customer wishes. In the event of an accident, the stored images can be reviewed and provide important information about the cause of the accident.
The camera can also be used for inspection
We see great potential in the railway camera as part of our offering, and it has more applications than just reversing trains. For example, the Swiss wagon hire company Wascosa is using the camera on its new ballast wagon to inspect the work on the opposite side of the wagon as it spreads ballast. This saves contractors time and money.
In March, the railway camera successfully passed its first test on a real train, and in the spring a pilot project was carried out with two cameras on a regular freight train.
Series production will start in Q2/Q3 2023.
Load lock sensor secures trailer trains
The load lock sensor checks that all the trailers in a freight train are correctly loaded. Since the serious accident on the Great Belt Bridge in 2019, there have been several similar incidents involving trailers on railway wagons.
With RMD’s solution, train drivers and traffic management can monitor in real time via the dashboard that all trailer wagons are properly locked.
The load lock sensor has huge potential and could even become a legal requirement.
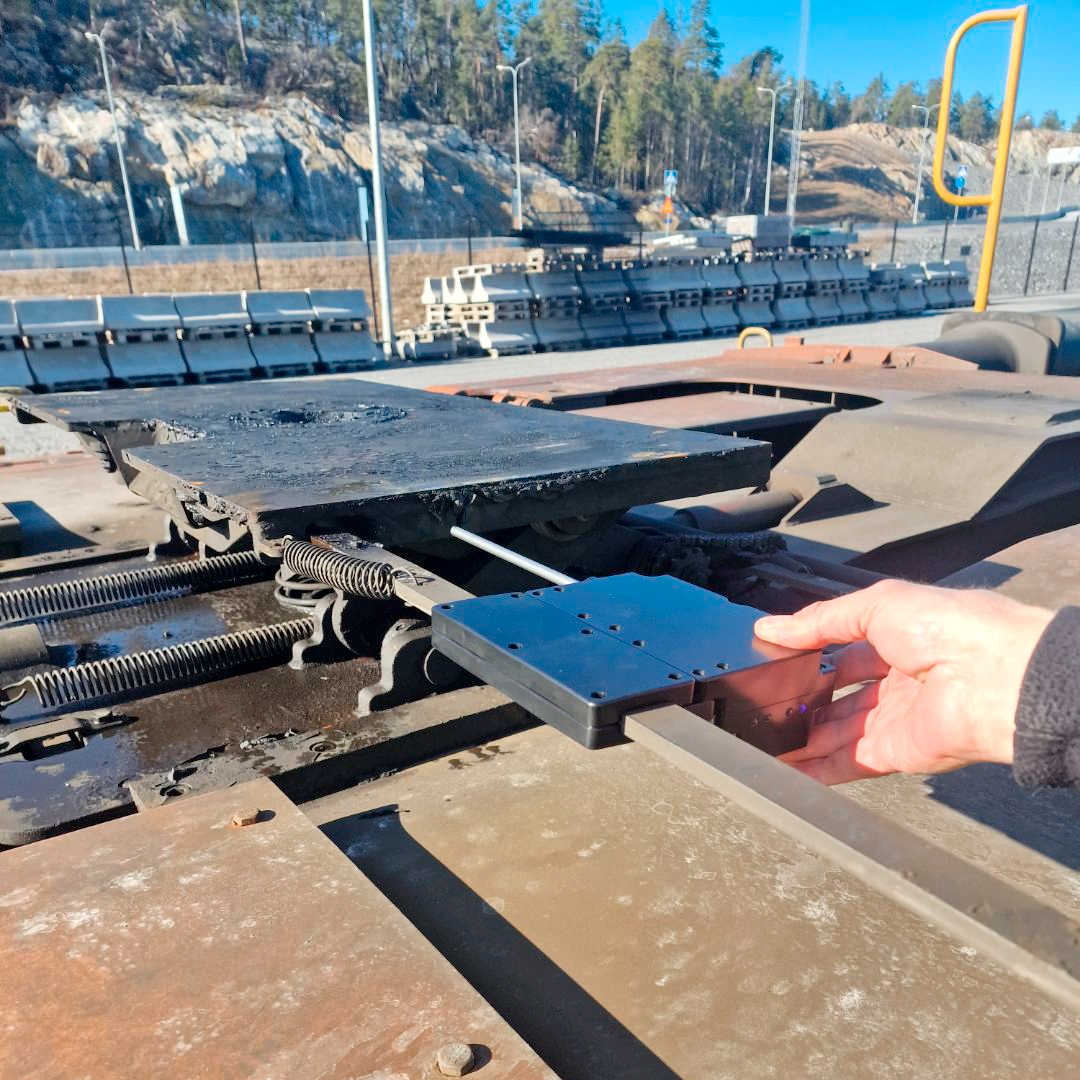
The RMD king pin sensor allows train drivers and traffic management to see in real time whether all trailer wagons are properly locked via the RMD dashboard.
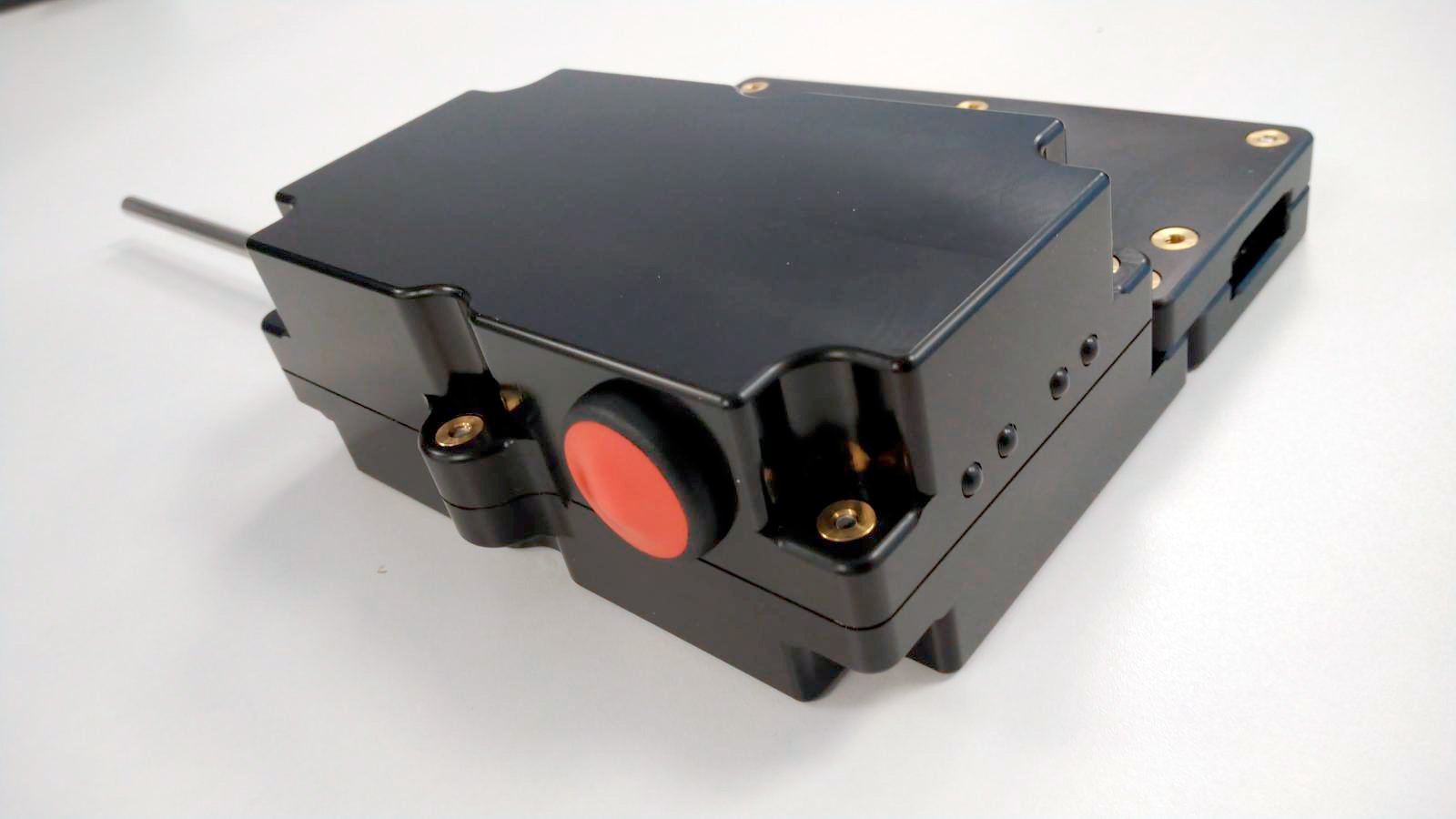
The king pin sensor, like the railway camera, is a natural extension of the surveillance platform.
Sensor that weighs freight trains automates invoicing
The Weight Sensor uses radar to monitor the weight of trains. It is a patented, state-of-the-art solution that will solve many challenges for both railway companies and infrastructure managers. Development of the sensor unit is in full swing and RMD expects to be able to carry out tests in a customer environment in autumn 2023.
The patent can be explained simply by the fact that radar units are used to measure the weight of a train’s load. The sensor continuously provides real-time data to RMD’s asset monitoring and management platform.
There are several clear benefits of load weight sensors for railway companies. Some of these are:
• Freight companies can automate invoicing.
• The possibility of overloading is eliminated, reducing both wear and tear on infrastructure and overcharging operators.
• Rail operators can be automatically charged the correct track access charge.
Catenary and wheel profile sensors
A recurring problem for railways, for example, is worn pantographs, which can grab the catenary and pull it down, causing long interruptions to train services. Overhead contact lines also wear over time and require regular maintenance.
One challenge is knowing when it is time for maintenance, so RMD provides better methods of identifying the condition of the pantograph and catenary so that maintenance can be carried out in a timely manner.
Radar units and accelerometers are used to measure various parameters between the catenary and the pantograph, providing data to RMD’s asset monitoring and management platform.
The wheel profile sensor is the latest addition to the family. This sensor is still under development. The sensor reads the wheel profile in real time to optimise wheel maintenance.
More news
RMD trains staff ahead of testing with Indonesia’s KAI
RMD has trained staff from its Indonesian partner Artindo to support the upcoming PoC with Indonesia’s KAI. The next step is a workshop with KAI in Bandung on 23 July.
RMD’s Rear-View Camera to Be Tested by US Freight Operator
RMD has delivered two test units to the United States for evaluation by a major American Class I freight railroad company. The cameras will be tested in full operation during switching work in terminal environments, with a particular focus on improving efficiency and safety.
RMD’s sensors to Indian Railways
Railway Metrics and Dynamics has signed an agreement with JK Exim for the testing and evaluation of PMU sensors with state-owned Indian Railways.